Understanding the Role of a Plastic Injection Mould Maker
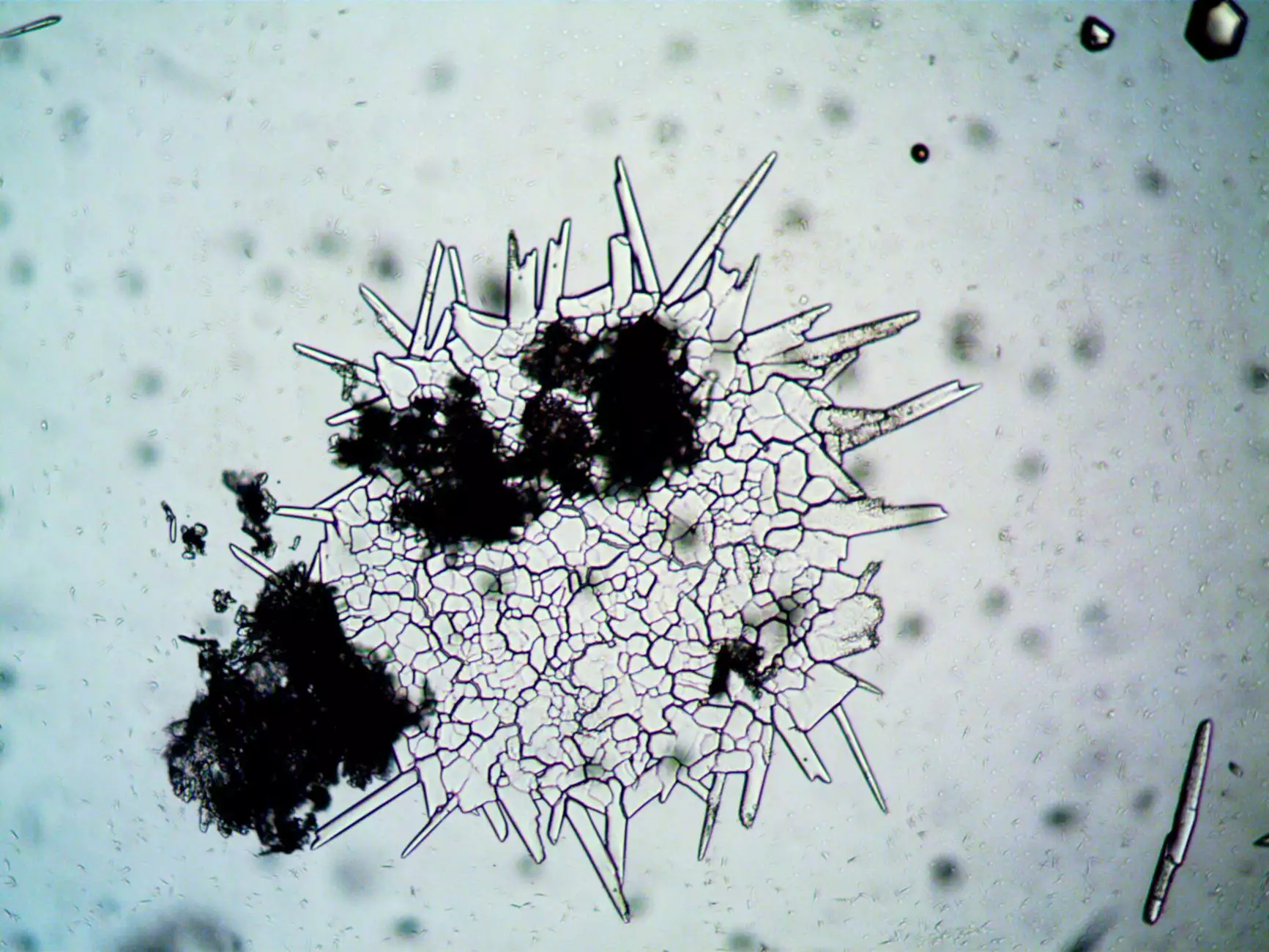
In today's competitive manufacturing environment, plastic injection mould makers play a critical role in the development and production of various plastic products. The process of plastic injection molding has revolutionized the way products are manufactured, providing efficiency and precision. This article delves into the intricacies of plastic injection molding, the essential qualities of a reliable mould maker, and how to choose the right one for your business needs.
What is Plastic Injection Molding?
Plastic injection molding is a manufacturing process that involves injecting molten plastic into a pre-designed mold, which then cools and solidifies into the final product shape. This method is widely used due to its ability to produce complex designs with high levels of accuracy and repeatability. The process is not only efficient but also cost-effective for large-scale production.
The Importance of Precision in Mould Making
At the heart of successful plastic injection molding is the mould itself. A well-crafted mould is crucial for maintaining the quality and consistency of the products. The precision involved in a mould's design dictates how well the molten plastic fills the cavity, influencing factors such as surface finish, dimensions, and tolerances. Therefore, choosing a proficient plastic injection mould maker is paramount.
Key Benefits of Partnering with a Professional Plastic Injection Mould Maker
Opting for a professional plastic injection mould maker comes with a host of advantages:
- Expertise and Experience: Experienced mould makers have refined their skills through years of practice and can troubleshoot issues effectively.
- Customization: A professional provider can offer tailored solutions that meet your specific product requirements and designs.
- Quality Assurance: They follow strict quality control measures throughout the manufacturing process to ensure each mould meets industry standards.
- Efficiency: Proficient mould makers can expedite the production process, reducing lead times and labor costs.
- Technology Integration: The top manufacturers leverage advanced technologies, such as Computer-Aided Design (CAD) and 3D printing, to enhance the precision and quality of the moulds.
The Process of Plastic Injection Mould Manufacturing
The journey of creating a plastic injection mould begins with design. Let’s explore the systematic approach taken by a skilled plastic injection mould maker:
1. Initial Consultation and Design
It all starts with a consultation where the client discusses their needs. Understanding the product, its functionality, and design aesthetics are crucial here. The mould maker usually employs CAD software to draft initial designs, translating ideas into digital formats.
2. Prototype Development
Before going into production, a prototype is often developed. This prototype is critical for testing the design and making any necessary adjustments before finalizing the mould.
3. Machining the Mould
Once the prototype is approved, the actual machining of the mould begins. High-precision CNC machines are used to carve the design into the metal blocks, ensuring that the cavities are formed accurately.
4. Testing and Quality Control
The mould undergoes rigorous testing to check for any design flaws. Quality control processes ensure that the finished mould conforms to the expected standards and performs optimally when producing the final products.
5. Production
After the mould passes the testing phase, it's ready for production. The plastic injection mould maker will oversee the entire injection molding process, ensuring that the Finished products meet specifications continuously.
Finding the Right Plastic Injection Mould Maker for Your Business
Choosing the right mould maker is crucial for the success of your manufacturing endeavors. Here are some essential tips:
- Research and Reviews: Begin by researching potential manufacturers. Look for reviews and testimonials from previous clients to assess their reputation.
- Portfolio Examination: Evaluate their portfolio to understand the types of products they specialize in and their manufacturing capabilities.
- Technical Expertise: Ensure that they have the necessary technical skills and experience to handle your specific requirements.
- Location: Consider the geographical location of the mould maker. Local suppliers may reduce shipping times and costs.
- Communication: Choose a manufacturer who communicates effectively and promptly. Open lines of communication are essential for successful collaboration.
- Cost and Value Analysis: While cost is a major factor, it’s essential to weigh it against quality and service. The cheapest option may not always be the best.
Conclusion: The Future of Plastic Injection Moulding
The future of the plastic manufacturing industry is bright, with continuous advancements in technology and materials. By selecting a skilled and reliable plastic injection mould maker, businesses can ensure they are not only keeping up with industry standards but are also positioned for future growth and innovation.
At Hanking Mould, we pride ourselves on our exceptional craftsmanship and dedication to quality. As a leading plastic injection mould manufacturer, we are committed to providing our clients with the best possible service and products.
Contact Us
If you are seeking a trustworthy plastic injection mould maker or need more information about our services, feel free to contact us. We would be delighted to assist you in your plastic molding needs and help you achieve your production goals.